UK Ag Brings Tobacco Stripping Mechanization Closer To Reality LEXINGTON, KY.
Burley tobacco is one of the most labor intensive crops a farmer could choose to grow. The stripping process often is the most laborious and tedious things about it, accounting for about half of the total labor cost. Traditionally, farmers manually remove the leaves from the stalks and then separate them into different grades for the market.
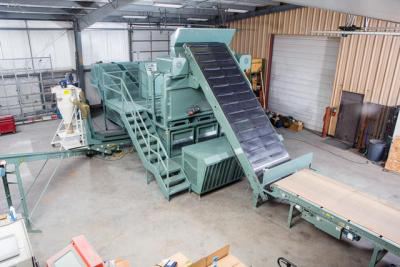
PHOTO: Steve Patton, UK Agricultural Communications Specialist
Agricultural engineers from the University of Kentucky College of Agriculture, Food and Environment have been trying to mechanize the stripping process for decades, and they finally have a machine they believe will lessen the burden for burley growers.
“About 30 years ago we first came up with some of these ideas for tobacco mechanization,” said George Day, agricultural engineer for UK’s Department of Biosystems and Agricultural Engineering. “Back then we were working on field harvesting as our primary goal, but we saw the need to mechanize the entire process.”
They started with mechanical harvesting and mechanical housing, and then the focus moved to mechanical market preparation. About three years ago, Day and fellow agricultural engineers Tim Smith and Larry Wells, powered with funding from Philip Morris International Management, were charged with trying to come up with a high-speed market preparation system.
“Our initial thoughts were always to try to go to what we refer to as a segmented stalk,” Day said. “Traditionally, producers went with an intact leaf. We thought of ways to try to cut the stalk and the leaf into 4-inch segments simultaneously and then use mechanical agitation, similar to a straw walker on a combine. We would then augment that with pneumatic separation which would allow us to buoy the lighter leaf material out of the heavier stalk material.”
Day said they’ve had some good success and have tested the machine on tobacco grower Doug Langley’s farm in Henry County. They were able to identify some shortcomings in the first system and modify it to come up with what they think is a viable option.
Don Fowlkes in the manager of agronomy for Phillip Morris. He was encouraged by what he and Day saw recently on Langley’s farm, which is in contract with Phillip Morris.
“If this were easy to do, it would have already been done,” Fowlkes said. “This particular technology doesn’t remove the whole leaf; it removes the leaf in pieces and makes it more feasible. The industry has to be able to purchase and use the product and so far, it’s looking promising.”
Day believes it’s very possible for the technology to be on the market within the next few years.
“We want to help try to keep burley production as viable as possible in Kentucky,” he said. “It is a highly labor-intensive crop, and if we can fine tune this and get it on the market, it’s really going to help Kentucky producers do their job in a more efficient way with less manual labor.”
Day expects the technology to significantly cut production costs. The economics of the system affect all levels of tobacco production. Preliminary indications show it could reduce the labor involved in market preparation by 75 to 90 percent.
“That is very significant and very important for the future of the U.S. burley tobacco market,” Fowlkes said. “If all the stars line up, I think we can see some of these manufactured and in the community in the next two years.”
Fowlkes was quick to recognize the importance of working with growers to get to this point.
“Without cooperators these things couldn’t happen,” he said. “We get some of our best ideas from farmers.”
Fowlkes envisions some of the larger operations implementing the technology first and then perhaps some type of centralized stripping operations being built, where farmers in a certain area can bring their crop and have it stripped.
UK agricultural engineers will demonstrate the new technology at the 50th National Farm Machinery Show in Louisville Feb. 11-14. ∆
|
|